Actually, I cut 3/4" stock quite a bit. I generally use a #10 blade for thick wood. The ones I use are Olson's FR408TW- Thick Wood and have only 7 TPI. They are thicker too, .018 and .080 width. The fewer teeth help to clear the saw dust easier so it doesn't build up and get the wood as hot as fast as the "more tooth" blades do.
As for making an inlay fit tight and flush, you need to stack cut the two pieces at the same time and tilt the table a bit so that the top of the upper piece is a bit larger than the top of the lower piece and then it fits into the void like a plug.
As far as "How much do I tilt the table?" The only way to find out is to do some practice cuts using the same thickness of wood as the project and cut a few small circles or shapes.
Different thicknesses cause the table tilt to vary. I usually start with 3 degrees tilt and after a practice cut or two will change it by about 1/2 degree at a time. Either add a 1/2 degree or subtract a 1/2 degree depending on how the cuts fit together.
I did an inlay of names on box tops for the grandchildren's Christmas gifts using 3/8" thick material.
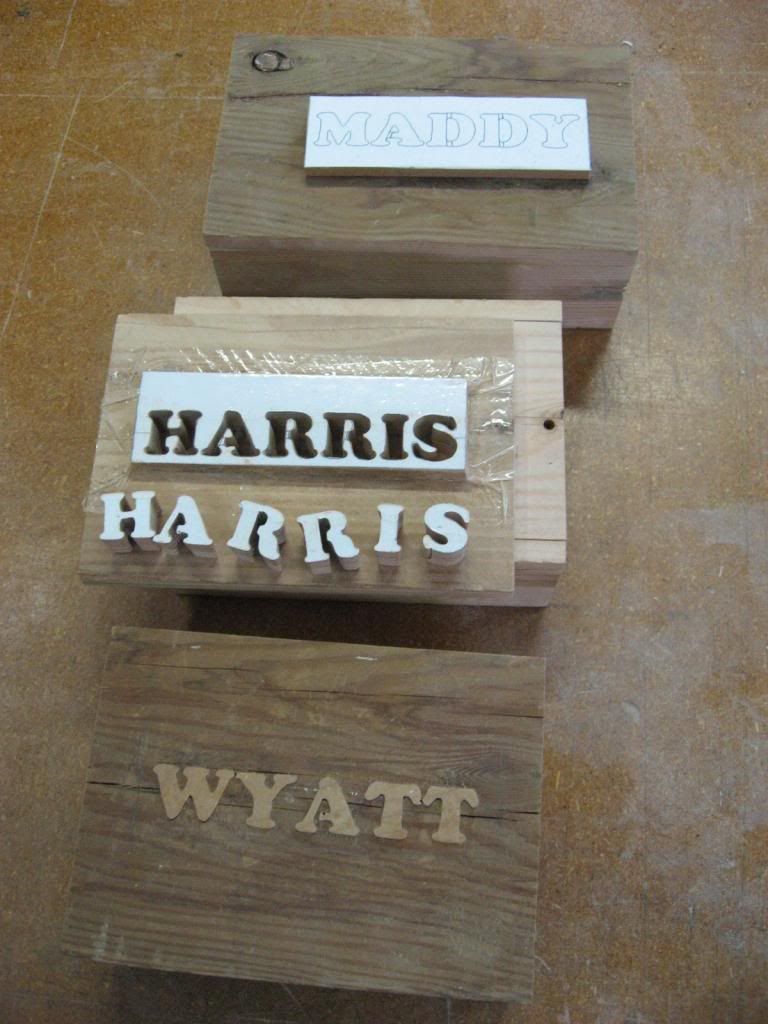
Thinner material will require a smaller blade and there for a different angle to the tilt too. I think I used a FD5 on this project.
Sometimes a picture is worth 1000 words.

Rog